LIMON set up business by producing LINEAR BUSHINGS, after years of development, we have owned a very good image and reputation in both domestic and overseas market. LINEAR BEARING is one of our strongest products, as a leading manufacturer in China, we have more than 20 years experience in the linear bearing manufacturing industry. LIMON linear bushing are of great quality, produced in our unique automatic workshop which is the first and only one in China. The size of our products widely range from diameter 4 up to 100mm, with various design versions. We also provide available options for diverse cage and coating.
Factory tour
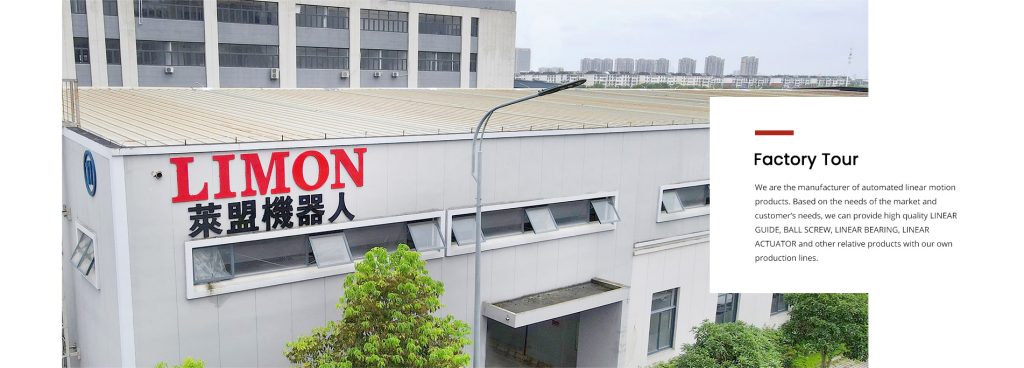
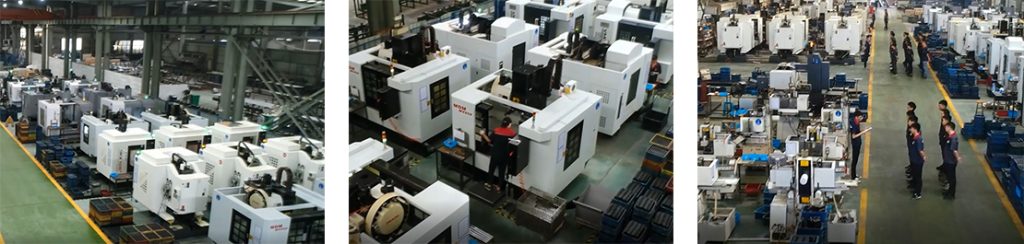
For the LINEAR GUIDE, LIMON is the biggest manufacture in China who have 18 production lines, 45,000 square meters area currently, now the monthly capacity for blocks is 300,000pcs, for rails it’s 70,000 meters.
With the increasing market demands, in 2020, we bought a new piece of land to expand our production base. The new facility will be put into use by the end of 2021, at that time our production line will increase to 30 and the capacity should be increased by 30-50% per year.
Our advantages for linear guide not only demonstrate through the powerful capacity, but also through the supply of various accessories and lubrication system, like ZZ/DD/KK.
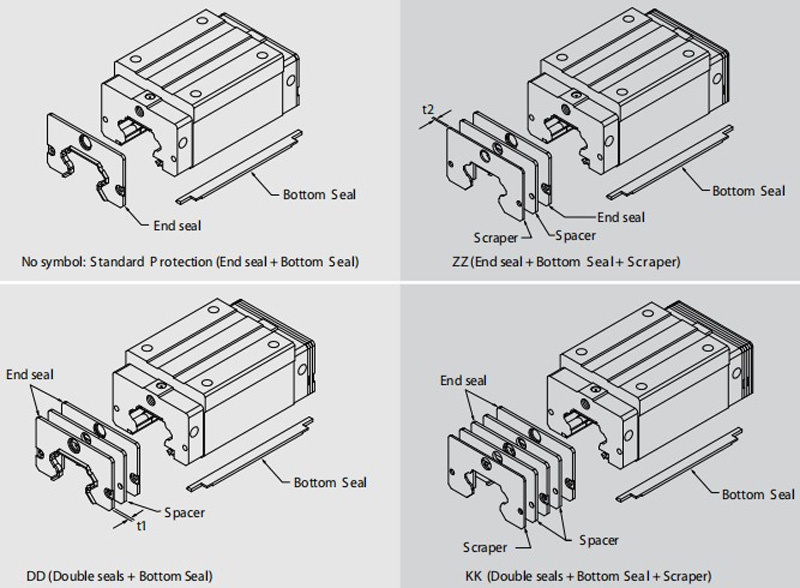
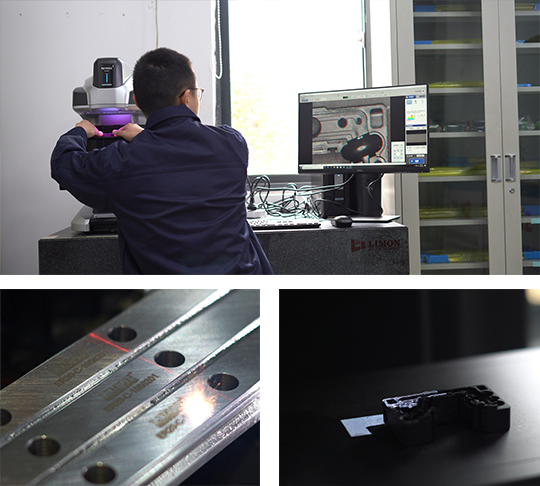
In 2020, we invested half a million dollars in a new block assembly workshop, which is constant-temperature and dust-free.
LIMON is committed to providing the best quality products to customers. Over the years, we have been constantly improving our production lines and product quality. We mainly invest in material, mold, equipment and technology. All the main raw materials are imported from Korea like other popular brands in this industry. Together with our professional Taiwan technical team and imported equipment.
We have great advantage in both production and sales of linear guide.
In terms of plant management,our factory adopts Japanese production workshop standard management, from incoming raw materials to the later production and processing, and then to period of testing, packaging, shipping, these are all under strict control.
Regarding to the BALL SCREW, as 16 production lines are available, our monthly capacity for nuts is 200,000pcs, for screws it’s 60,000meters. This capacity will be double after our factory expanding project finished by the end of 2021, and we expect it to increase by 30-50% per year.
We can provide both rolled and grind type ball screw, the precision can reach up to C3. The size ranges are from 12 to 80mm, with left and right turning, and double nut is also available. We provide our partner customized solution. In the past ten years, we have provided customized ball screw and non-standard machining for many automation & CNC equipment.
The process from raw material to finished products is all under the quality control, including straightness, noise testing, precision inspection and so on. To ensure the quality, we invest constant temperature workshop for grinding, and the integrated heat pipe road is arranged to ensure that the accuracy of the product due to temperature changes is minimized. We also built a temperature constant workshop for testing, after a lot quality inspections and comparisons, our products is proved to have very good noise performs.
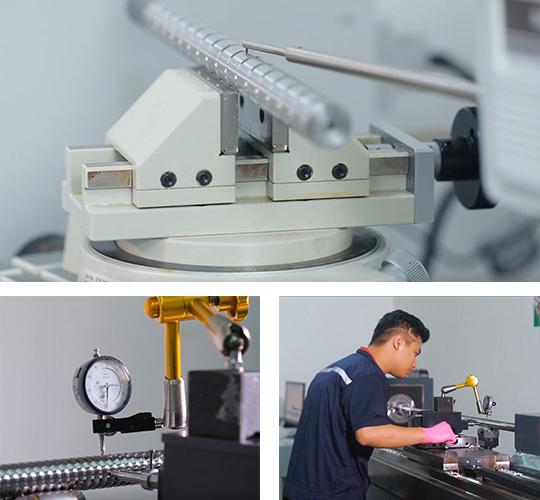
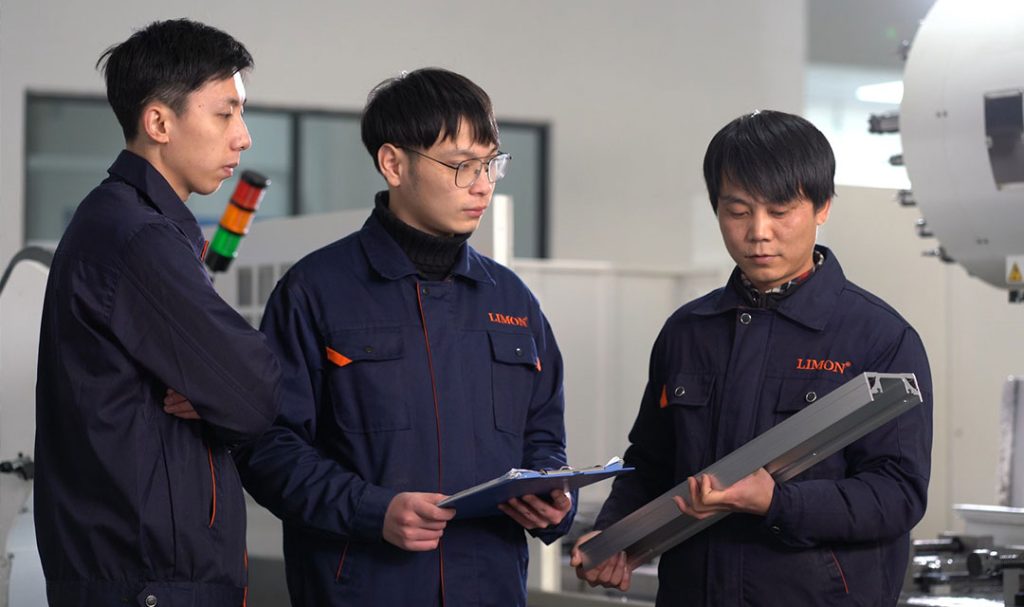
For the LINEAR ACTUATOR, both ball screw driven and belt driven type are available. It is easy to assemble, and also can be used in the clean room of protection class 10. Besides, our design is really flexible and can be installed in multiple directions according to the actual conditions of customers.
We have been working with our Taiwan engineers since 2012, through years we keep making continuous efforts to improve our management and work efficiency, and focusing on providing customers better communication experience and quicker service support.
Besides, we attach great importance to the production and quality of our products, our QC system allows us to retrospect all the incoming to outgoing process. And there is a separate inspection room for external purchased accessories, after quality testing passed, it will being placed and well managed in our warehouse.
We have focused on manufacturing for many years, good quality also have a lot to do with factory’s equipment capability. LIMON has been in linear unit industry for so many years, we are more than capable of doing simple processing of raw materials, to the cutting and straightening of internal guide ball screw, milling and drilling of external Aluminum profiles, and then to the assembly of the unit, we have professional equipment and personnel for each production line and professional technical team to guide each process.
Quality is the mission of the market, the detection of finished products is very important, we also invested in a clean and quiet testing room for detection. When technician finished assembly, there will be professional inspector to inspect and make the testing report, also the data will be recorded in LIMON system.

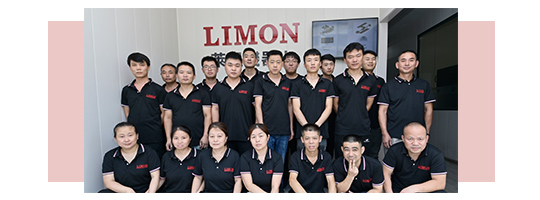
This is LIMON, your reliable partner. We are firmly dedicated to the linear system field, we will always keep the passion to make innovations, and provide high efficient service for you.